Minimizar os tempos de produção para garantir a competitividade é um dos desafios mais importantes da indústria automotiva – Henry Ford já reconheceu isso há mais de um século. Após décadas de otimização, é difícil reduzir ainda mais os tempos de usinagem, mantendo o mesmo nível de qualidade. No entanto, a empresa Volkswagen (VW), perto da cidade alemã de Kassel, conseguiu isso na produção de caixas de câmbio usando as retificadoras de engrenagem KAPP NILES.
A fábrica da Volkswagen na pequena cidade de Baunatal é uma das maiores plantas alemãs da empresa, com uma força de trabalho de cerca de 17.000 colaboradores. Atualmente, sua produção concentra-se principalmente em caixas de câmbio para automóveis de passageiros em dez séries diferentes. Centros de engrenagens de KAPP NILES estão sendo implantados em 50% das linhas de fabricação. A empresa, com sede em Coburg, Baviera, é conhecida principalmente como especialista em retifica por geração com ferramentas dressáveis – um processo que combina produtividade e qualidade.
880 Caixas de Câmbio por Dia
As máquinas KAPP NILES também são utilizadas na produção da caixa de câmbio DL 382 de dupla embreagem para Audi. Um total de dezesseis engrenagens são necessárias para trocar as sete marchas com este tipo de caixa de câmbio – dez retificadas e seis processadas por honing. A unidade de produção trabalha 24 horas por dia, 5 a 6 dias por semana, dependendo da demanda. A VW se esforça para atingir um valor EPEI de 1 dia na unidade de produção. EPEI significa „every part every interval – cada parte a cada intervalo“, o que significa que todos os componentes podem ser produzidos cada dia para a caixa de velocidades mencionada. Este tipo de produção simplificada requer processos contínuos e um alto grau de flexibilidade. O funcionário técnico, Christian Hahn, é o responsável pelo processo de produção da caixa de câmbio DL 382 de dupla embreagem.
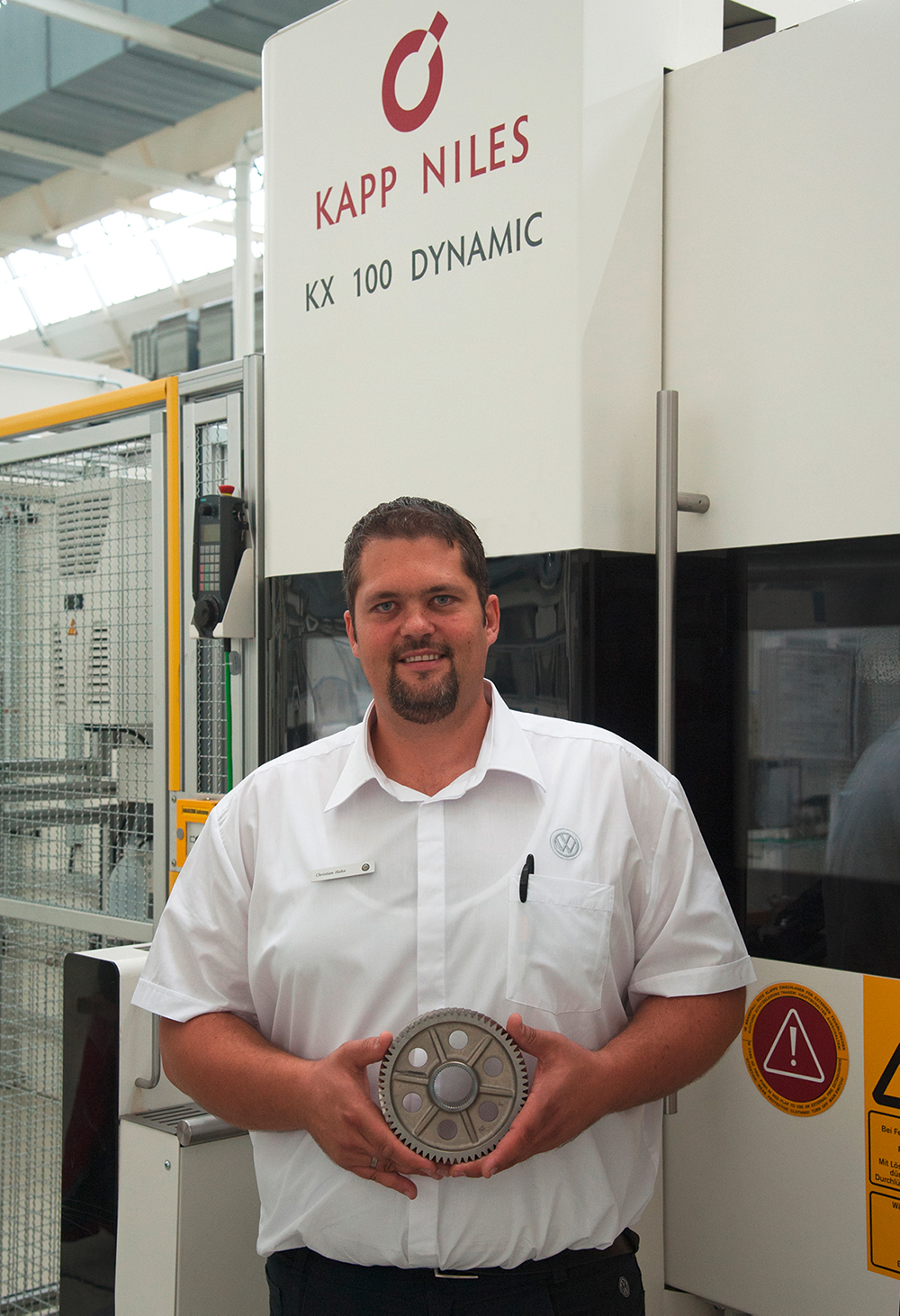
Ele descreve o processo de produção; „Temos cinco centros de engrenagens da KAPP NILES na unidade de produção de coroas e mais dois na unidade de produção de pinhões. Para atingir um valor EPEI de 1 dia, trocamos de peça na máquina da unidade de produção de coroas duas vezes por dia. Assim, podemos produzir dez diferentes por dia.“
O desafio da produção flexível foram os tempos de ciclo curtos; com uma produção de 880 caixas de engrenagens por dia, uma máquina na produção de coroas deve produzir 1.760 peças por dia. Incluindo todos os tempos de setup e falhas, isso resulta em um tempo de ciclo da linha de 34 segundos. Um tempo médio de ciclo de linha é de cerca de 39 a 40 segundos. Bernd Kümpel, técnico de aplicação da KAPP NILES, analisa estes números: „Economizar 5 a 6 segundos por ciclo não parece muito no início, mas juntos podem ser uma redução de até 15%. Se eu considerar que pelo menos 40% dos segmentos não podem ser influenciados, tenho que reduzir o tempo real do processo em 30-40%. Visto desta forma, 34 segundos é um verdadeiro desafio.“
Economizando Segundos Preciosos Durante a Troca, Dressando e Medindo
Um total de sete máquinas KAPP NILES estão sendo implantadas que, com sua baixa necessidade de espaço, são ideais para a produção altamente automatizada da Volkswagen. Estas incluem: Três KX 100 DYNAMIC, duas KX 260 TWIN na produção de coroas e duas KX 160 TWIN na produção de pinhões.
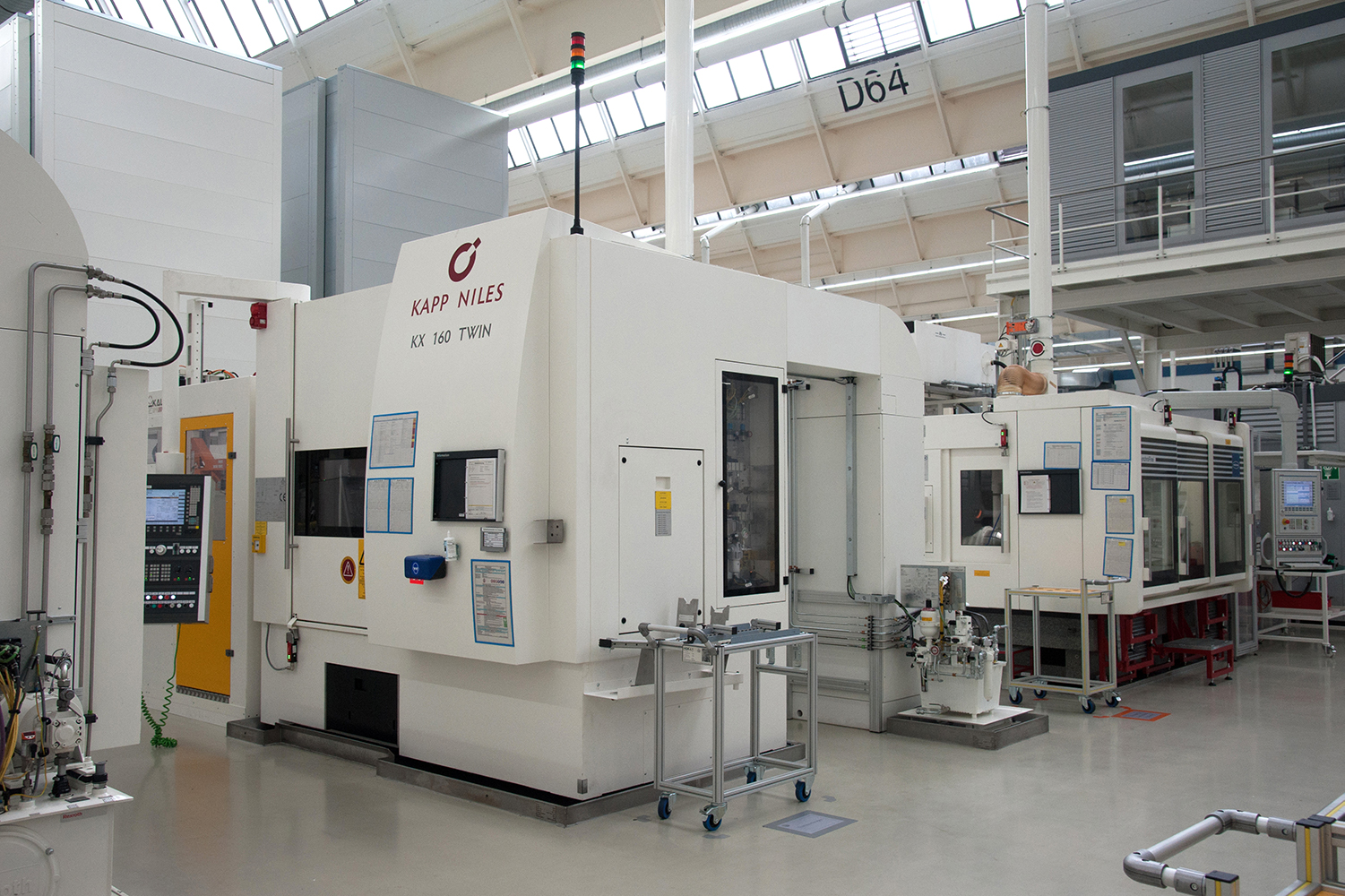
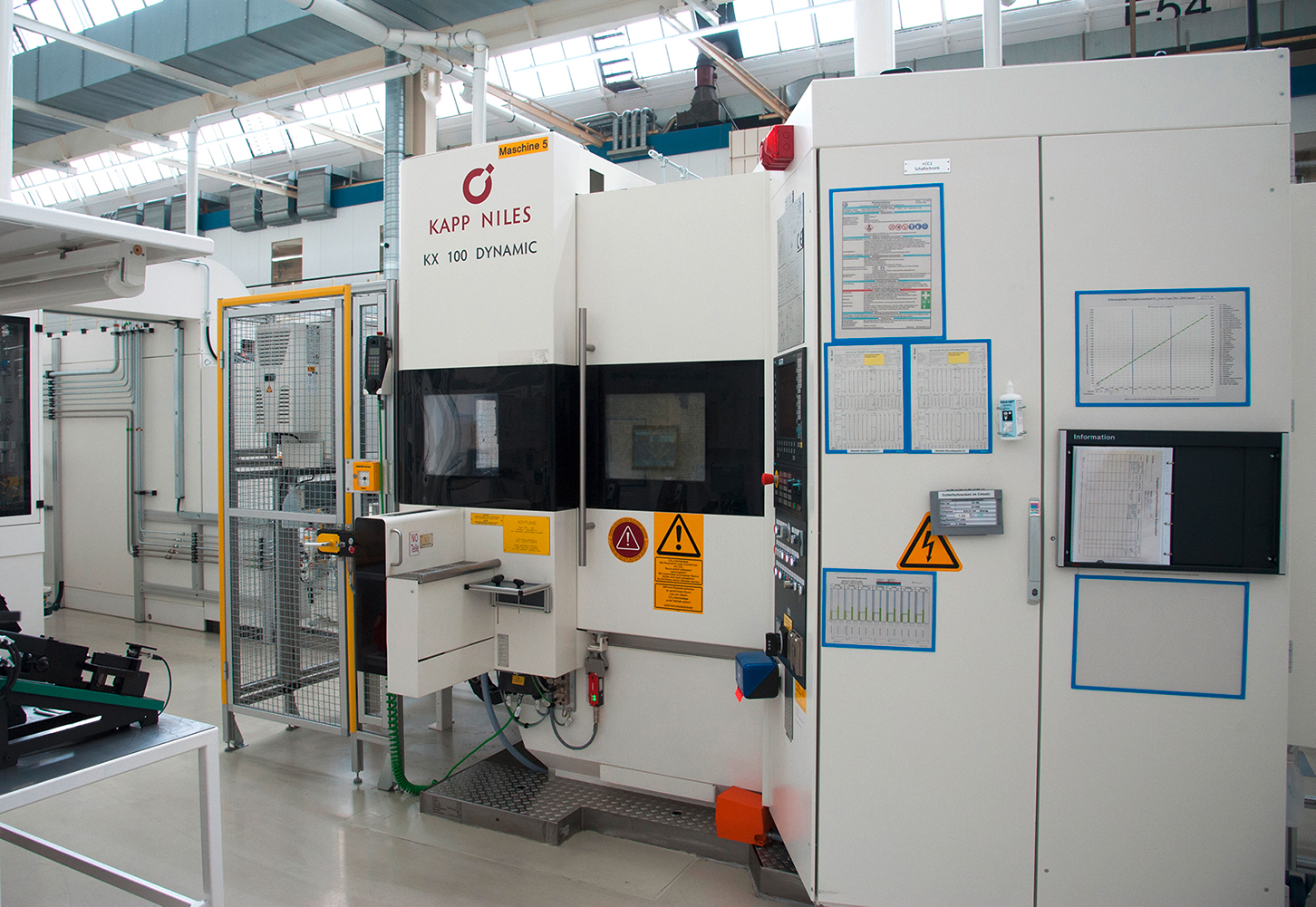
Christian Hahn e Bernd Kümpel concordaram desde o início que o tempo de ciclo desejado só poderia ser alcançado com uma combinação de várias medidas. Para minimizar o esforço diário de setup, Christian Hahn se certifica de que as coroas que serão produzidas em uma máquina tenham furação do mesmo tamanho. Portanto, ele tem que ajustar a máquina, mas não as ferramentas de fixação. O tempo de setup restante é minimizado pelo conceito de configuração inteligente da KX 100 DYNAMIC. Para uma máquina, ele precisa de apenas 20-25 minutos. “A configuração semiautomática torna a KX 100 DYNAMIC extremamente fácil de usar“, diz Bernd Kümpel, descrevendo o processo. „Tudo o que você precisa é de uma chave Allen para toda a operação de setup. Com ela, você opera o mandril expansivo de fixação hidráulica do rolo dressador. Todo o resto é conectado sem parafusos por meio de interfaces HSK (HSK = cone de eixo oco) “. Um auxílio visual adicional está disponível na forma de um ciclo guiado por menu e fácil de entender no painel de comando da máquina. Ao concluir o processo passo a passo e acompanhar na tela de confirmação, o operador garante que nenhuma etapa do processo seja executada incorretamente ou, de fato, esquecida. Falhas de alto custo são evitadas dessa forma.
As ferramentas são dressadas com rolos de perfil completo, permitindo que todas as roscas do caracol cilíndrico sejam aproximadas e moldadas simultaneamente. Assim, com um rolo de perfil completo de 5 entradas, o tempo de dressagem pode ser reduzido em mais da metade sem comprometer a qualidade.
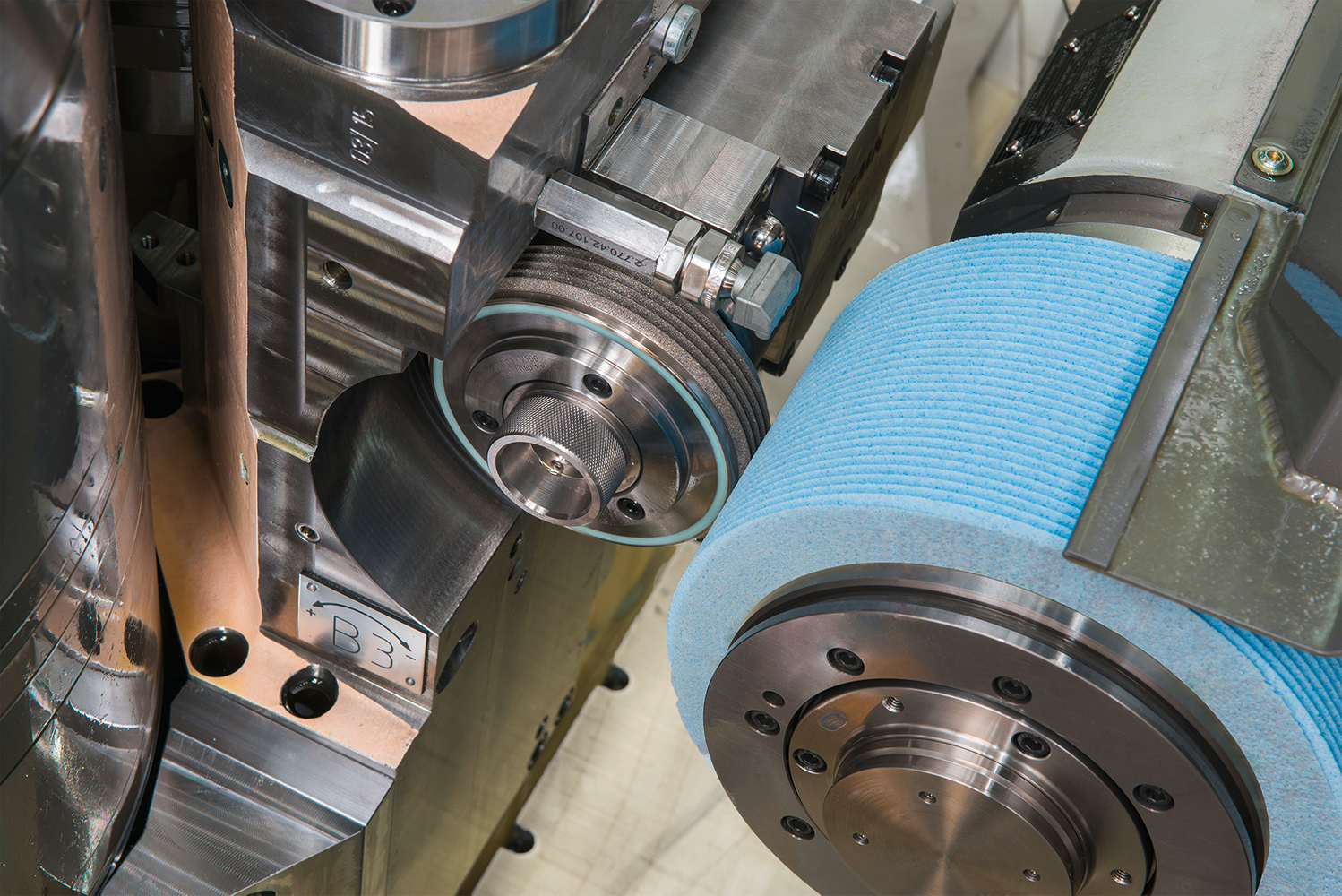
O sistema de medição integrado é outra importante economia de tempo. Christian Hahn explica a vantagem; „Após cada troca, uma medição de qualidade deve ser feita fora da máquina. Na verdade, continuamos exigindo isso, mas já posso verificar os parâmetros básicos relacionados à qualidade com o sensor de medição integrado na própria máquina. Isso economiza muito tempo, pois podemos iniciar a produção antes que os resultados da medição externa estejam disponíveis.“ O sistema de medição integrado das máquinas KAPP NILES acelera consideravelmente o processo de reinicialização. A medição externa apenas verifica mais dentes e gera o relatório de medição para monitorar a engrenagem.
Aberto para Nova Tecnologia de Máquina-Ferramenta
A busca pelo potencial de otimização também inclui o próprio processo de retificação. As ferramentas Cubitron ™ II da 3M ™ mostram uma abordagem altamente promissora, com arestas de corte geometricamente definidas de formato triangular, em comparação com rebolos convencionalmente dressáveis. Christian Hahn enumera os benefícios dessas ferramentas: „Com isso, você pode subir um degrau, para dizer com clareza. Ou seja, remover mais material em um passe e remove-lo mais rápido.“
Para este propósito, a KAPP NILES forneceu um trabalho preparatório relevante com um grande número de testes de retificação internos para poder usar os benefícios desta ferramenta com os componentes DL 382. Bernd Kümpel; „Com o CII, você pode remover uma quantidade considerável de cavacos sem nenhum dano térmico ao componente. Dessa forma, reduzimos o consumo de tempo em sólidos 30% em comparação com outras retificadoras, dependendo da peça. “
Economizando Espaço e Dinheiro
A produção é caracterizada por uma esteira (ou correia) que atravessa todo o pavilhão.
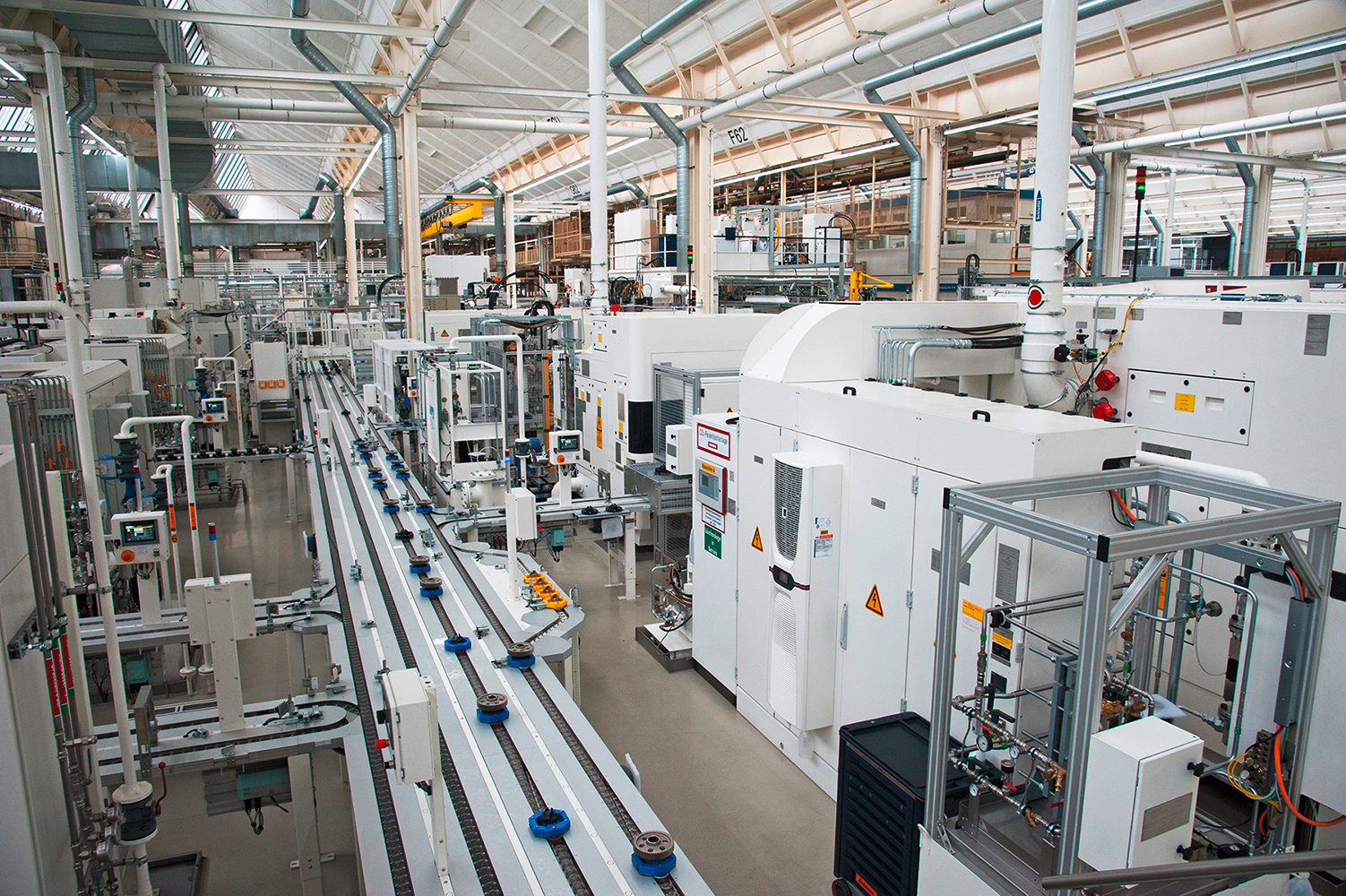
Entre os colaboradores, ganhou o apelido de „rodovia expressa“. O espaço disponível é limitado. Portanto, as máquinas altamente compactas KX 100 DYNAMIC são a escolha preferida. Este tipo de máquina tem duas colunas rotativas montadas separadamente, cada uma com eixo de coleta verticalmente móvel com um fuso porta peça. Enquanto uma peça está sendo usinada, o outro eixo pick-up descarrega a peça usinada e carrega uma peça não usinada no fuso porta peça. A peça a ser trabalhada é alinhada fora da área de trabalho. Isso permite que o fuso da peça, já acelerado até a velocidade de usinagem, seja basculado para a área de trabalho. Os tempos não produtivos são, portanto, reduzidos ao mínimo.
Uma unidade de transferência (Fig. 6) faz a carga e descarga da esteira transportadora.
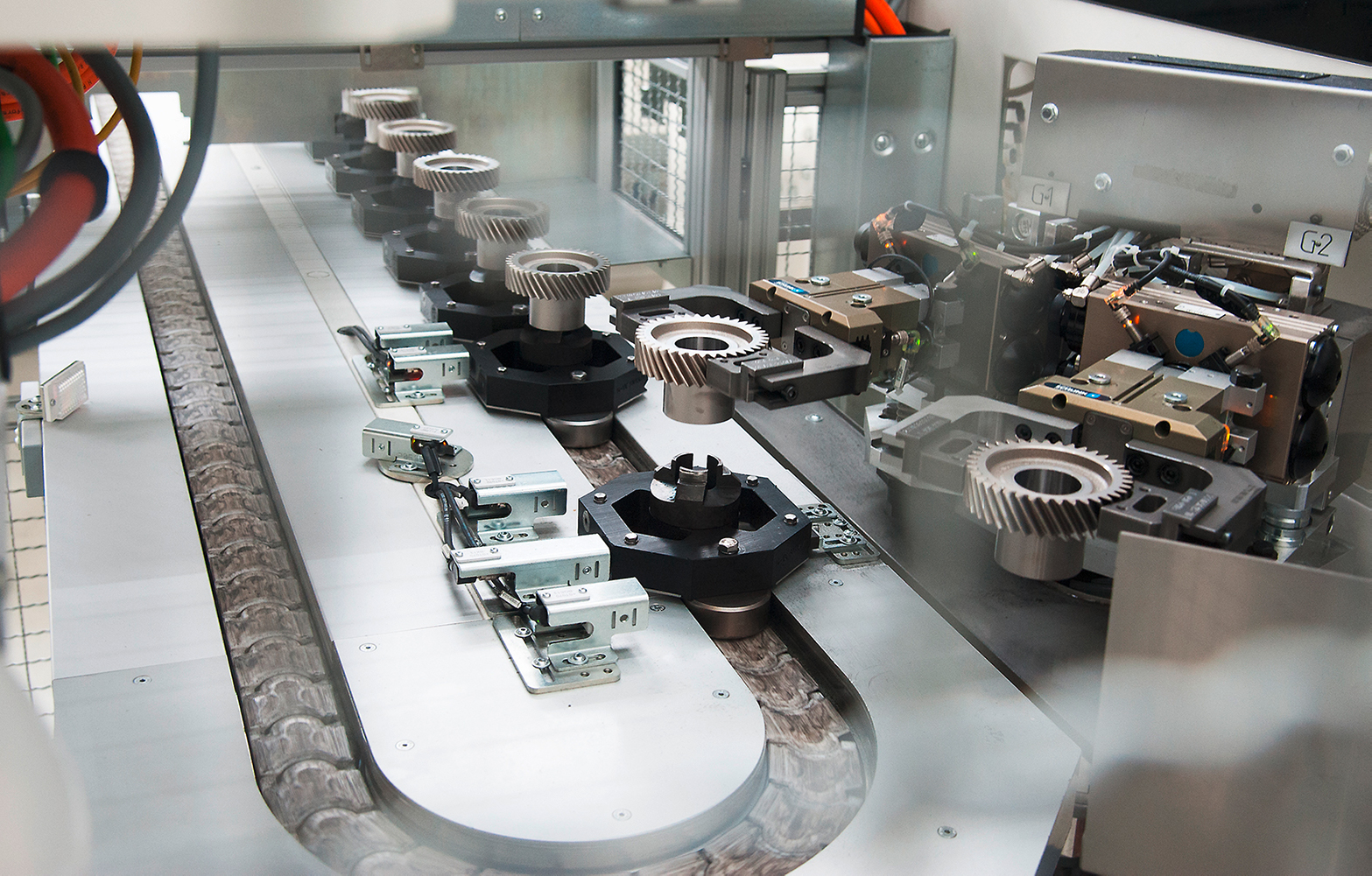
Bernd Kümpel nos diz; „Normalmente posicionamos a esteira diretamente abaixo da máquina. No entanto, isso não foi possível aqui. Com a unidade de transferência, compensamos a altura e a distância da esteira à máquina.” Esta solução não é apenas compacta, mas também econômica. „Uma solução de automação integrada teria sido significativamente mais cara, cerca de 25% do preço da máquina“, acrescenta Bernd Kümpel. „Uma unidade de transferência simples custa menos de 10% do preço da máquina.”
Sucesso Planejado
O tempo para conversões e instalação é, na maioria dos casos, muito limitado. Mas os objetivos altamente ambiciosos foram alcançados. Christian Hahn faz um balanço; „Durante todo o processo, fiquei muito satisfeito com o suporte em nossa planta e o serviço local. Ficamos convencidos com o conceito da máquina e conseguimos superar todos os obstáculos juntos. O tempo de ciclo, em particular, era um aspecto crítico. Mas, nós conseguimos.” E para isso, eles enfrentaram muitas restrições de tempo. A instalação que incluiu a análise de capacidade da máquina, onde 100 componentes de cada tipo são produzidos e medidos a 100%, ocorreu no verão de 2016. A produção começou logo na primeira semana de setembro.
Além do tempo de ciclo, outras dificuldades foram superadas na produção de pinhões.
Christian Hahn o descreve da seguinte maneira; „Os pinhões são ocos e, portanto, comparativamente instáveis. Isso exigia uma técnica de fixação especial e uma máquina que pudesse absorver as vibrações inevitáveis no processo de retificação. A KX 160 TWIN pode fazer isso devido ao seu design e construção sólida que, por sua vez, ajudam a alcançar uma melhor qualidade de retificação.”
Para o caso de ser necessário um serviço imediato, a KAPP NILES destacou um funcionário em Kassel que fornece suporte apenas para a fábrica da Volkswagen. Bernd Kümpel diz; „Nossa maior prioridade é garantir a produção, independentemente dos problemas que ocorram.“ Suporte excepcional muito apreciado pela VW.